Exploring the World of Plastic Housing Manufacturers
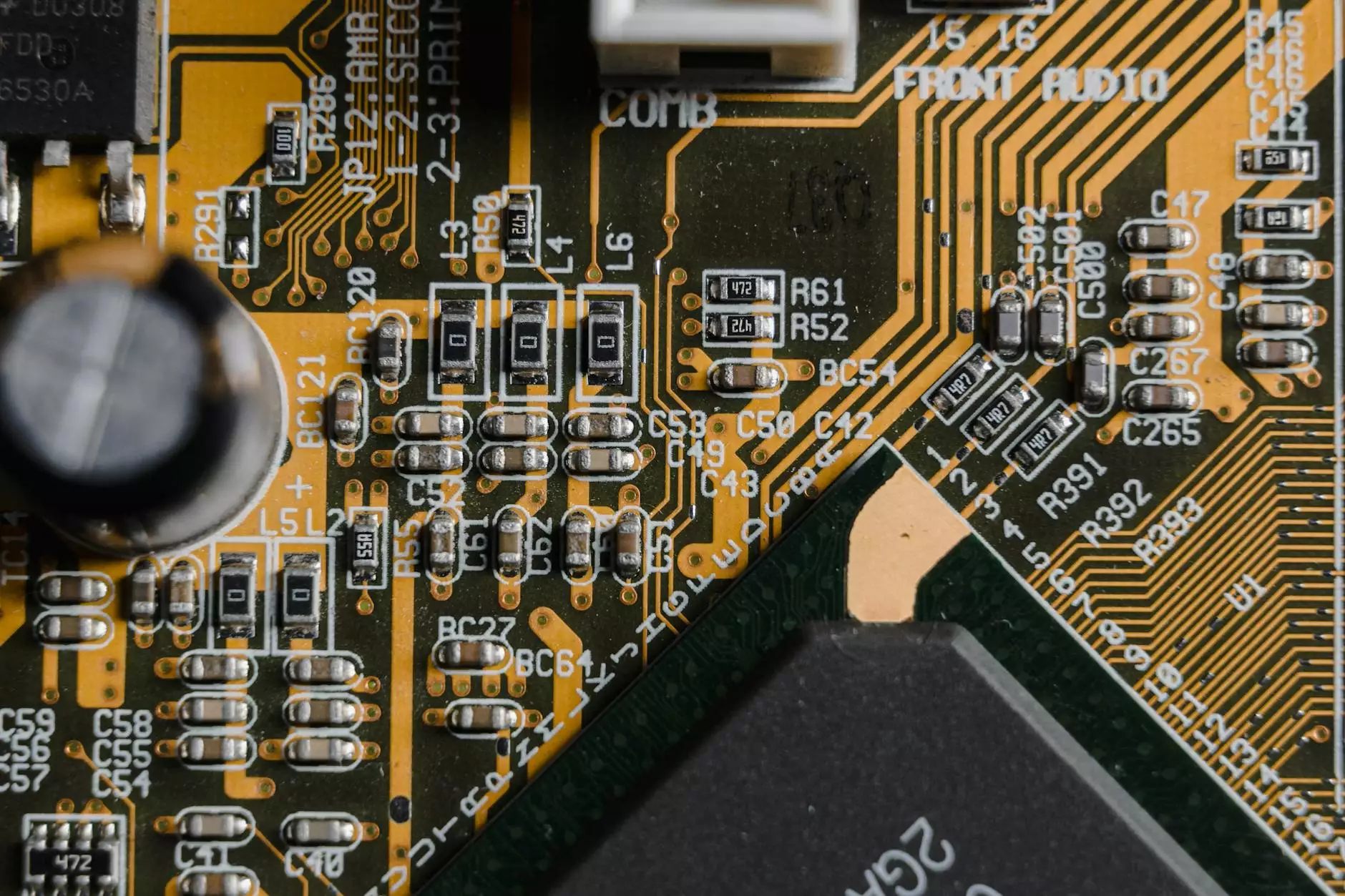
In today's rapidly evolving technological landscape, the role of plastic housing manufacturers has never been more critical. With the demand for lightweight, durable, and cost-effective solutions, these manufacturers are at the forefront of innovation, creating products that cater to various industries, from electronics to automotive and beyond.
What are Plastic Housings?
Plastic housings are protective enclosures designed to safeguard electronic components or mechanical systems. They are crafted from various types of plastics, each offering unique properties that contribute to the overall functionality and durability of the product. The versatility of plastics allows manufacturers to customize designs, shapes, and sizes to meet specific requirements.
The Importance of Plastic Housing Manufacturers
Plastic housing manufacturers play a vital role in bridging the gap between technological advancements and practical applications. Their contribution can be observed in several key areas:
- Cost Efficiency: Utilizing plastic materials often results in reduced production costs compared to metal or composite alternatives.
- Weight Reduction: Plastic housings are significantly lighter, which is crucial for industries such as aerospace and automotive where every gram counts.
- Corrosion Resistance: Plastics do not corrode, providing longevity and reliability in various environments.
- Design Flexibility: Manufacturers can create intricate shapes and designs that enhance both functionality and aesthetics.
Key Types of Plastic Used in Manufacturing Housings
Plastic housing manufacturers utilize a variety of thermoplastics and thermosetting plastics. Here are some of the most common types:
1. Polycarbonate (PC)
Polycarbonate is known for its exceptional strength and impact resistance. It is often used in electronic housings that require a transparent cover, allowing visibility of internal components.
2. Acrylonitrile Butadiene Styrene (ABS)
ABS is a popular choice due to its lightweight nature and toughness. It's widely used in consumer electronics and automotive parts.
3. Polypropylene (PP)
Polypropylene is resistant to many chemical solvents, bases, and acids, making it ideal for housing applications in the medical and automotive fields.
4. Polyethylene (PE)
Polyethylene is versatile and is often used in less demanding applications where flexibility and durability are necessary.
Innovative Manufacturing Techniques
To stay competitive, plastic housing manufacturers have adopted innovative techniques that enhance production efficiency and product quality:
- Injection Molding: A widely used manufacturing process that allows for mass production of identical parts with high accuracy.
- 3D Printing: This technology enables rapid prototyping and the creation of complex geometries that were previously impossible to manufacture.
- Blow Molding: Utilized for hollow plastic components, this technique is commonly applied in creating bottles and containers.
- Thermoforming: This process involves heating a plastic sheet until pliable and molded into a desired shape, ideal for packaging and product housings.
Applications of Plastic Housings
The application of plastic housings is diverse, reflecting the challenges and requirements of various industries. Here's an overview:
1. Electronics
In the world of electronics, durable and lightweight plastic housings are essential for protecting sensitive components from environmental factors. Many consumer gadgets and devices utilize plastic housings due to their aesthetic appeal and functionality.
2. Automotive
The automotive industry uses plastic housings in numerous components, including dashboards, electronic control units, and lighting systems. The shift towards lighter materials in vehicles enhances fuel efficiency and performance.
3. Medical Devices
Plastic housings are crucial in medical devices as they provide the necessary protection against contamination and environmental hazards. The use of biocompatible plastics ensures safety for patients.
4. Telecommunications
Telecom equipment often requires robust housings that can withstand harsh weather conditions. Plastic housings offer the blend of durability and lightweight properties essential for outdoor installations.
Benefits of Working with Experienced Plastic Housing Manufacturers
Choosing the right plastic housing manufacturer is paramount for ensuring product quality and performance. Here are the key benefits:
- Technical Expertise: Experienced manufacturers bring a wealth of knowledge and expertise that can guide product development and optimization.
- Customization: The ability to customize designs specific to your industry's requirements can lead to greater satisfaction and better end products.
- Quality Assurance: Reputable manufacturers adhere to strict quality control processes, ensuring reliability and consistency in production.
- Innovation: Collaboration with manufacturers at the forefront of technology can provide insights into the latest trends and materials in the industry.
Sustainability in Plastic Housing Manufacturing
With growing environmental concerns, the plastic industry is actively seeking sustainable practices. Plastic housing manufacturers are increasingly adopting eco-friendly measures, such as:
1. Recyclable Materials
Many manufacturers are exploring ways to utilize recycled plastics, thereby reducing landfill waste and the need for virgin materials.
2. Biodegradable Plastics
Research and development in biodegradable plastics offer exciting prospects, allowing for environmentally conscious products without sacrificing performance.
The Future of Plastic Housing Manufacturing
The future looks promising for plastic housing manufacturers, driven by advancements in technology and growing market demands:
- Integration of Smart Technologies: As smart devices become more prevalent, manufacturers will need to innovate housing designs to accommodate new functionalities.
- Enhanced Manufacturing Processes: Continued advancements in automation and AI will streamline production, leading to even higher efficiency and lower costs.
- Focus on Sustainability: With sustainability becoming a priority, the push towards greener manufacturing practices will shape the future landscape of the industry.
Conclusion
In conclusion, the role of plastic housing manufacturers is pivotal in various industries, providing essential solutions that enhance product performance and durability. The innovations in materials, manufacturing processes, and a focus on sustainability position these manufacturers to meet the challenges of the future. As the industry continues to evolve, collaboration and forward-thinking will remain key drivers of success, ensuring that plastic housings not only protect but also pave the way for a smarter, more efficient world.