Cement Silo 100 Ton: A Comprehensive Guide to Efficiency and Durability
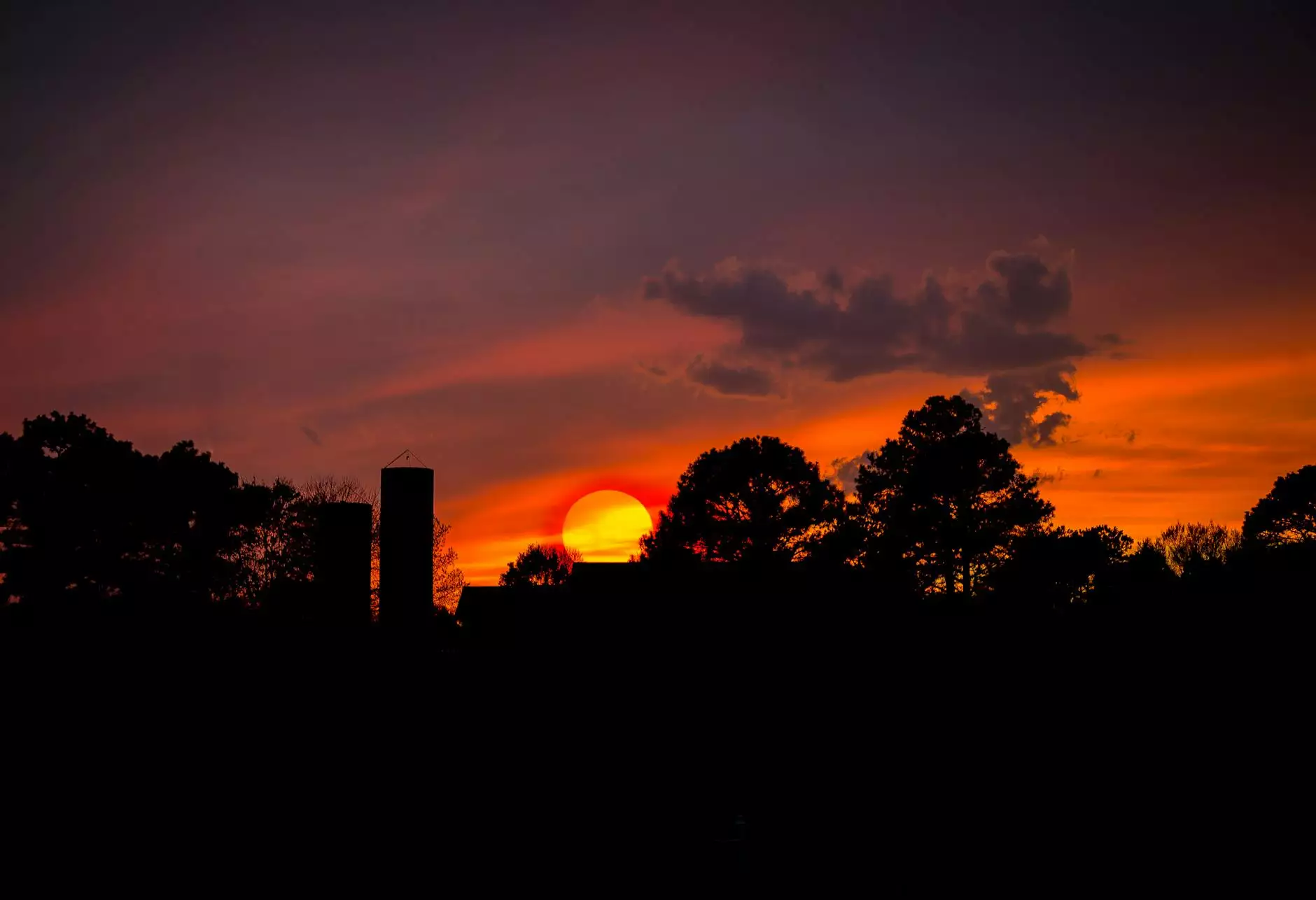
The construction industry is ever-evolving, placing demands on businesses to utilize efficient and reliable equipment. For companies dealing with concrete and other bulk materials, the cement silo 100 ton has become a cornerstone of operational efficiency. This article delves deep into the importance, features, and benefits of implementing a 100-ton cement silo into your operations.
Understanding the Cement Silo
A cement silo is an essential storage vessel that holds bulk cement and other powdered materials safely and efficiently. Typically, cement silos come in various sizes, but the 100-ton capacity is particularly popular due to its ability to balance storage needs with space constraints.
Key Features of the 100 Ton Cement Silo
- Robust Design: Made from high-quality materials to withstand harsh environmental conditions.
- Efficient Loading and Unloading: Designed for easy access to maintain smooth material transfer processes.
- Advanced Safety Features: Incorporates techniques to prevent overfilling and ensures structural integrity.
- Mobility Options: Some models offer transport options, allowing for relocation as project needs change.
- Minimal Footprint: Perfect for locations with limited space while maximizing storage capacity.
Why Choose a Cement Silo 100 Ton?
The choice to invest in a cement silo 100 ton is driven by multiple operational advantages. Here are several reasons why this silo capacity is advantageous:
1. Increased Storage Capacity
When managing large construction projects or manufacturing processes, having a 100-ton silo allows for a substantial amount of material to be stored. This reduces the need for frequent deliveries, which can be both time-consuming and costly.
2. Cost Efficiency
Purchasing materials in bulk generally reduces overall costs. A 100-ton cement silo enables businesses to buy larger quantities, benefiting from wholesale pricing and minimizing wastage.
3. Enhanced Process Flow
With a silo on-site, the process of mixing and transporting cement becomes seamless. This enhances the workflow on job sites, reducing delays associated with loading and unloading materials.
4. Improved Inventory Management
Tracking inventory becomes simpler with a dedicated silo. Companies can monitor their usage rates and plan replenishments, ensuring they never run out of essential materials.
5. Environmental Sustainability
On-site silos help reduce the carbon footprint associated with transporting cement to various job sites frequently. By consolidating storage, companies contribute to environmental protection while maintaining operational effectiveness.
Installation Process of a Cement Silo 100 Ton
The installation of a 100-ton cement silo is a vital phase that requires careful planning and execution. Here's an overview of the steps involved:
Site Preparation
Before installation, it's crucial to select a suitable location that can accommodate the weight and size of the silo. The site must also provide easy access for delivery trucks and maintenance teams.
Foundation Construction
The silo needs a sturdy foundation to support its weight. This usually involves concrete pouring, which should be allowed to cure properly before erecting the silo.
Erection of the Silo
Depending on the type of silo, it may be delivered in sections and require assembly on-site. Crane services are often utilized for this purpose.
Connecting the Silos
After erecting the silo, it must be connected to the relevant machinery, such as feed hoppers and conveyor systems, ensuring a smooth flow of materials.
Safety Checks
Before the silo becomes operational, a series of safety checks should be performed. This includes confirming structural integrity and ensuring all safety features are functional.
Maintenance of Cement Silo 100 Ton
Proper maintenance of a cement silo 100 ton is crucial to ensure longevity and optimal performance. Regular inspections and care can prevent significant issues over time.
Regular Inspections
Establish a routine for inspecting the silo for any signs of wear, cracks, or corrosion. Early detection of issues can save money in repairs and prevent hazardous situations.
Cleaning Procedures
It's essential to maintain cleanliness inside the silo to prevent material contamination. Residue from previous materials can affect the quality of current mixes.
Monitoring for Moisture
Moisture can lead to clumping of cement; therefore, it is important to monitor and control humidity levels within the silo. Installing moisture monitoring devices can facilitate this process.
Choosing the Right Provider for Cement Silos
When considering a cement silo 100 ton, it is vital to select a reputable manufacturer. The provider should offer quality assurance, comprehensive support, and excellent customer service. Below are parameters for choosing the right supplier:
1. Industry Reputation
Research the manufacturer’s track record in supplying silos. Reviews, testimonials, and case studies can provide insights into their reliability.
2. Customization Options
Every project has specific needs; therefore, a good provider should offer customizable silo options to fit your operational requirements.
3. Warranty and Support
A trustworthy manufacturer will stand behind their products, offering warranties and maintenance support to ensure your investment is protected.
Conclusion
Investing in a cement silo 100 ton is a strategic decision that can enhance operational efficiency, reduce costs, and improve overall project management in the construction and manufacturing sectors. By understanding the various aspects of cement silos and partnering with a reliable supplier, businesses can ensure they are well-equipped to meet the demands of the industry.
Ready to elevate your storage solutions? Visit Polygonmach.com for expert insights and premium equipment that meets the highest industry standards.