The Power of Dip Molding Silicone in Modern Business
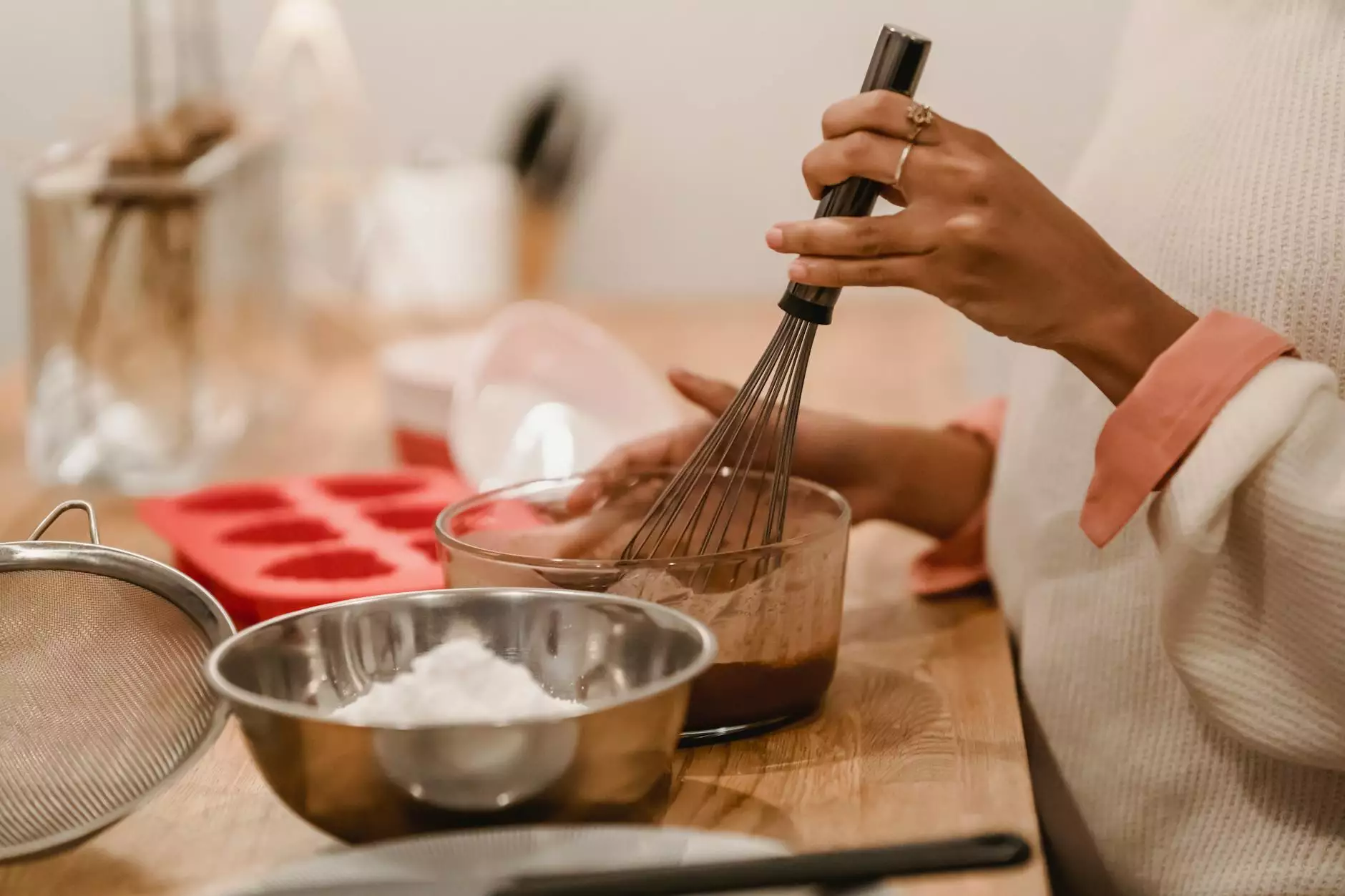
In today's rapidly evolving industrial landscape, the demand for innovative manufacturing processes has never been greater. One such process that has gained significant traction is dip molding silicone. This technique not only enhances product durability but also contributes to design flexibility, making it a preferred choice across various sectors, particularly in electronics and medical supplies. In this comprehensive article, we will delve into the ins and outs of dip molding silicone, exploring its benefits, applications, and future trends that businesses like nolato.com can leverage for growth and success.
Understanding Dip Molding Silicone
Dip molding silicone is a specialized technique used to create rubber-like coatings on various substrates. This method involves immersing a mold into liquid silicone, which then cures to form a flexible, durable, and resilient layer. The unique properties of silicone—such as high-temperature resistance, chemical stability, and excellent electrical insulation—make it an ideal material for numerous applications.
The Process of Dip Molding
The dip molding process involves several key steps:
- Mold Preparation: The creation of a mold is the first step. This mold is typically made from metal or other heat-resistant materials designed to withstand the curing process.
- Dipping: The prepared mold is then dipped into liquid silicone. The depth and duration of the dip determine the coating thickness.
- Curing: Once dipped, the silicone is cured, often through baking, to solidify the coating into its final form.
- Demolding: After curing, the coated mold is carefully removed, revealing a finished silicone product.
Benefits of Dip Molding Silicone
Businesses engaging in the use of dip molding silicone can derive numerous benefits, which include:
- Versatility: Dip molding silicone can be applied to a wide variety of substrates, including metal, glass, and plastic, allowing for diverse applications across industries.
- Durability: The resulting silicone coatings are highly resistant to environmental factors, including UV light, temperature fluctuations, and chemical exposure.
- Flexible Design Options: The process allows for intricate designs and varied thicknesses, enabling customization to meet specific product requirements.
- Electrical Insulation: Silicone is an excellent electrical insulator, making it ideal for use in electronic components that require secure and reliable operation.
- Sustainability: Silicone is a more environmentally friendly material when compared to other plastics, as it can be produced with eco-conscious practices and has a longer life cycle.
Applications in Electronics
The electronics industry is one of the principal sectors benefiting from dip molding silicone technology. Below are some common applications:
1. Protective Coatings
Many electronic devices require protective coatings to safeguard delicate components from moisture and dust. Silicone provides an impervious barrier that is essential for maintaining device functionality.
2. Wire Insulation
Silicone can coat wires and connectors, providing excellent protection against electrical shorts and ensuring safe operation in various environments.
3. Keypads and Switches
Dip molded silicone is widely used in the production of keypads for electronics, offering a comfortable feel and reliable functionality while being resistant to wear and tear.
Applications in Medical Supplies
The medical supplies sector utilizes dip molding silicone in various vital aspects:
1. Medical Device Covers
Many medical devices require protective covers that are soft to the touch while still providing durability and safety. Dip molding silicone achieves this ideal balance effectively.
2. Seals and Gaskets
Silicone gaskets and seals are crucial in medical devices to maintain sterility and prevent contamination. Their durability and chemical resistance ensure that they perform reliably under challenging conditions.
Future of Dip Molding Silicone in Business
The future of dip molding silicone appears promising, with several trends shaping its evolution:
1. Advancements in Materials
Research and development are continuously improving silicone formulations, offering enhanced properties such as greater flexibility, strength, and resistance to additional environmental factors.
2. Growing Market Demand
As industries increasingly recognize the benefits of silicone, the market for dip molding silicone is expected to expand, leading to more innovations and applications.
3. Eco-Friendly Practices
With a growing interest in sustainability, businesses are likely to gravitate towards eco-friendly production methods, making silicone a popular choice.
Why Choose Nolato for Your Dip Molding Silicone Needs?Nolato is at the forefront of dip molding silicone technology, offering unmatched expertise and a commitment to quality. With a focus on both the electronics and medical supplies sectors, Nolato provides tailored solutions that meet the specific needs of its clients. Their dedication to innovation, sustainability, and customer satisfaction positions them as a leader in the field.
The Conclusion
In summary, the utilization of dip molding silicone across electronics and medical supplies is transforming how products are manufactured and designed. This versatile material not only enhances product durability and functionality but also opens doors for innovative designs that were previously unfeasible. As businesses seek to improve their offerings, adopting dip molding silicone could be the key to standing out in a competitive market. With strong partners like nolato.com, companies can leverage the advantages of dip molding silicone to not only meet but exceed market expectations.
As we advance into a future driven by technology and innovation, understanding and harnessing the potential of dip molding silicone could very well determine the leaders of tomorrow's economies. Stay ahead by embracing these advanced manufacturing techniques to ensure your business not only meets industry standards but sets them.